Recently, VASEY designed and engineered a new air duct system after a paint booth fire, saving the manufacturer more than $250,000 in additional cost and downtime required to purchase and install a brand-new system.
Unfortunately for the customer, VASEY only became involved after the fire. A fire that could have been avoided with an ongoing preventive maintenance program.
The unit was nine feet square by three feet high. The booth was constructed of 16-gauge sheet metal with welded seams. There were no CAD drawings. Everything had to be engineered to specifications on-site.
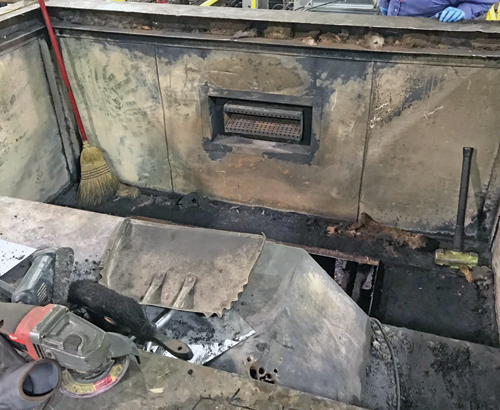
Cut-away Section of Booth before Rebuild
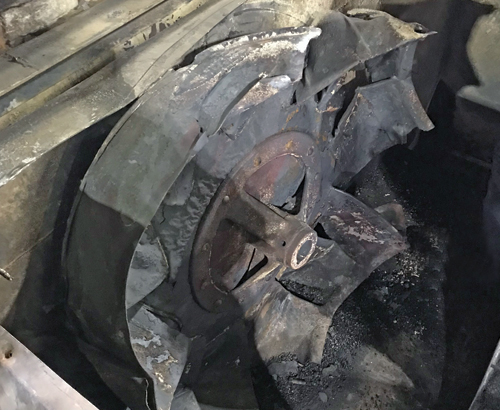
Cone Shaped Opening in the Ductwork in Front of the Fan Blower
First, VASEY chiseled away at the paint build up with chipping hammers and removed burnt batt-type insulation – a long, tedious, and dirty job. Once the top of the paint booth was opened and cleaned, the existing steel panels were removed and replaced with 16-gauge welded steel panels, making it stronger since the old panels warped from the excess heat build-up.
With nothing more than the original opening dimensions, VASEY designed and engineered a new system for the paint drying booth – new panels (4-inches thick consisting of a 16-gauge, welded, metal casing and insulation), and industrial-style fan (with a maximum heat capacity up to 250°F) were installed in the original opening.
Once the new panels were in place, VASEY created an access door so maintenance could crawl inside for easy clean out. The new system now runs safely and efficiently at 140°F.
VASEY manufactured a custom filter rack, consisting of over 50 filters that maintenance can easily swap out. Initially four men were on-site for demolition. During the rebuild phase, there were primarily two men working on the system 12-hours per day. After six weeks we had our client’s system back up and operating at full speed.
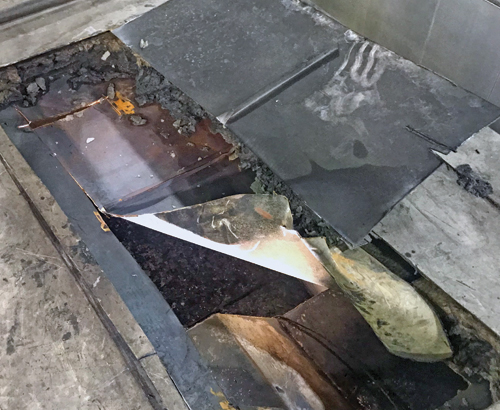
Opening after the Fire Department Cut Holes in the Paint Booth
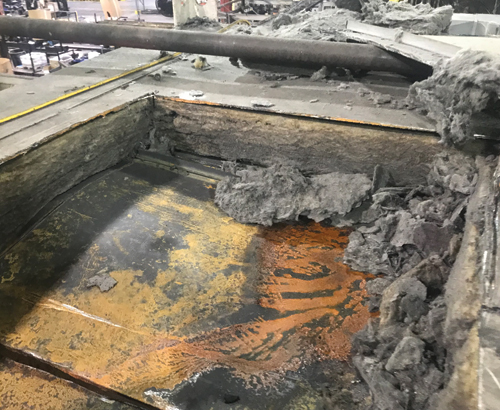
Affected Area After all the Ductwork and Insulation are Removed
“The fire could have been easily avoided with proper training and ongoing preventive maintenance.”
– Danny Marshall, VASEY Project Manager
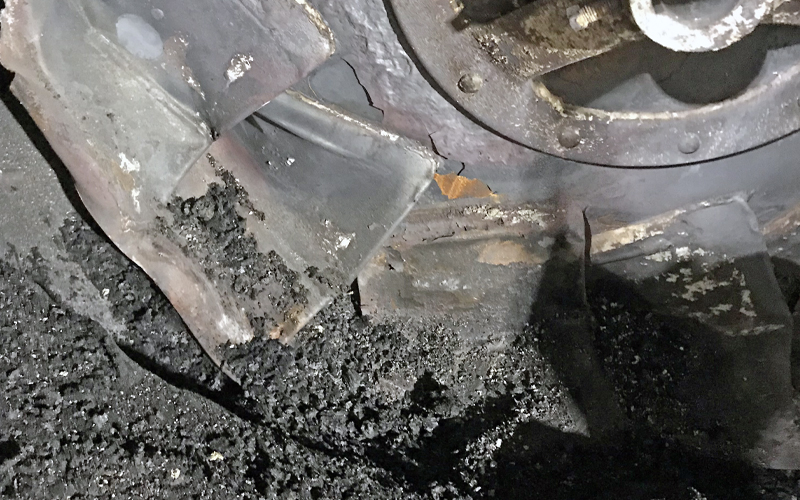
This is the cone-shaped opening of the blower housing (above). Return air passed through this location where all the paint particles were pulled through the system. The outer edge shows previous build up and our client’s attempt to try and scrape off paint build up. Everything was funneled back into the blower where particles were picked up and pushed back through and down into the paint booth ductwork.
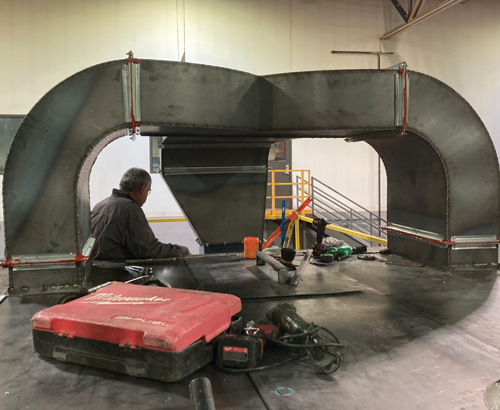
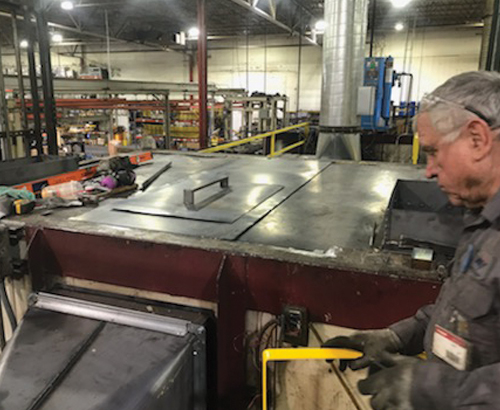
We custom designed and installed a brand new ductwork system (above – right) in addition to new openings and access areas for easier preventive maintenance. New top part of the system with the new panels in place. Notice the access door (above – left). Client’s maintenance team can now access the ductwork to clean the system.
Guaranteed Lifetime Protection (GLP) and Preventive Maintenance (PM) Programs
Benefits Include
- Extend facility and equipment life
- Lower utility bills
- Experience fewer breakdowns
- Achieve optimal comfort conditions
- Eliminate unexpected capital expenditures
- Obtain predictable maintenance and operation costs
- Gain peace of mind
- Ensure one affordable annual fee