Client Overview
A global market leader in container manufacturing, specializes in creating sustainable and reusable logistics packaging solutions. With over 70 years of experience, the container manufacturer provides a wide range of plastic pallets, customizable boxes/containers including collapsible, folding, hazardous goods, large capacity, nestable, stackable, thermoforming and more. With eight locations over three continents, the container manufacturer expertly serves industries such as automotive, electronics, retail, pharmaceuticals, and textiles.
Their specialties include Thermoforming, Injection Molding, Customized Solutions, Pallets, Top Caps, ESD Solutions, Home Delivery Solutions, Bulk Containers, Straight Wall Containers, AIAG RC-9 SLC Containers, Automation Totes and Trays – AS/RS Solutions.
The company prides itself on its commitment to sustainability, utilizing 100 percent recyclable plastics to create innovative solutions for various industries.
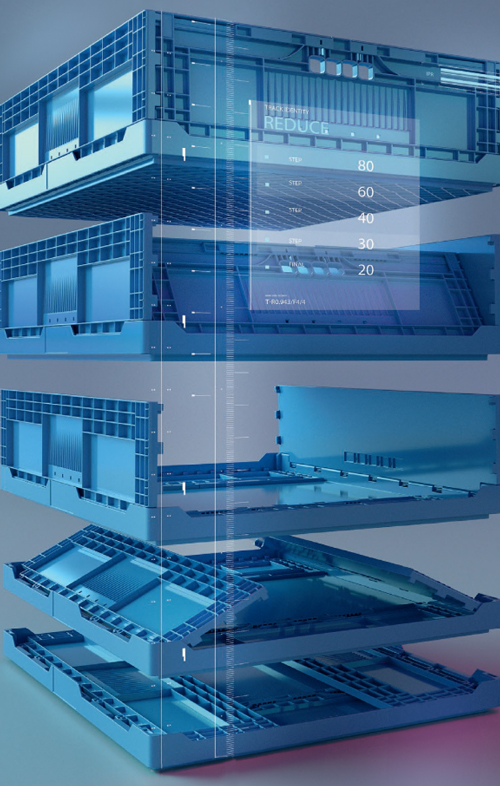
The Challenge
The manufacturer’s newly expanded injection molding facility in Southern Indiana, faced a severe setback when their crucial ONI chiller, an energy-optimized system vital for production, became stranded in a shipping container mid-transit across the Atlantic Ocean.
This unforeseen logistics issue threatened to disrupt their production timeline, jeopardizing the manufacturing of millions of dollars’ worth of products. Since the expanded facility housed six new injection molding machines scheduled to operate round the clock, a solution was urgently needed to minimize downtime and avoid missing critical shipping deadlines.
Project Execution
To address an urgent situation, the manufacturer turned to VASEY, a trusted partner known for its expertise in solving complex industrial challenges. VASEY swiftly devised a multi-phase solution to mitigate the impact of the logistical crisis and ensure the seamless operation of the facility.
First Solution
VASEY procured a temporary 225-ton chiller and seamlessly integrated it into the expansion facility’s infrastructure. VASEY’s team efficiently installed permanent piping connections, enabling the temporary chiller to step in and ensure that production could begin while awaiting the arrival of the stranded ONI chiller. Once the ONI chiller arrived, VASEY set the new chiller in place.
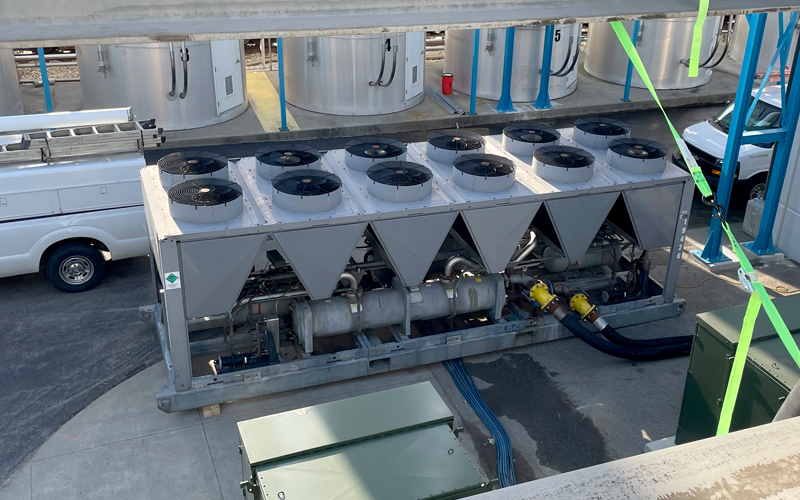
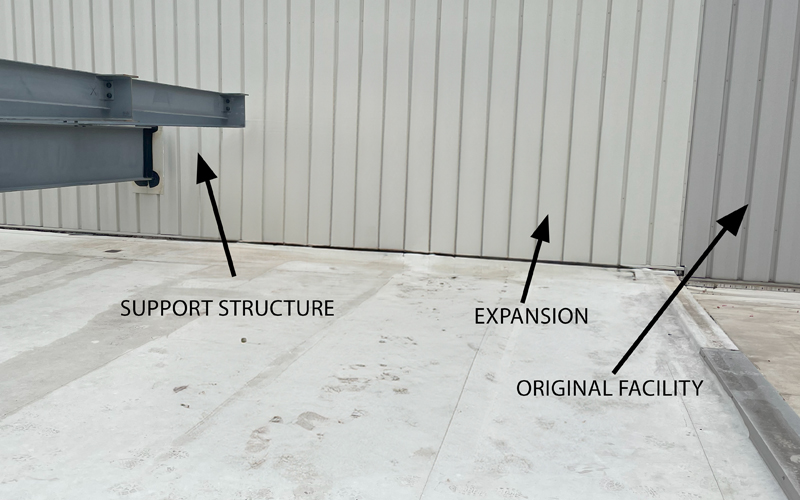

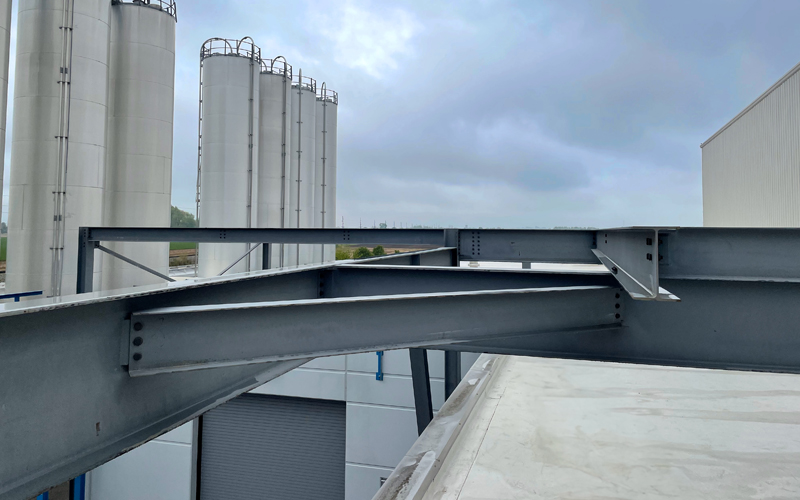
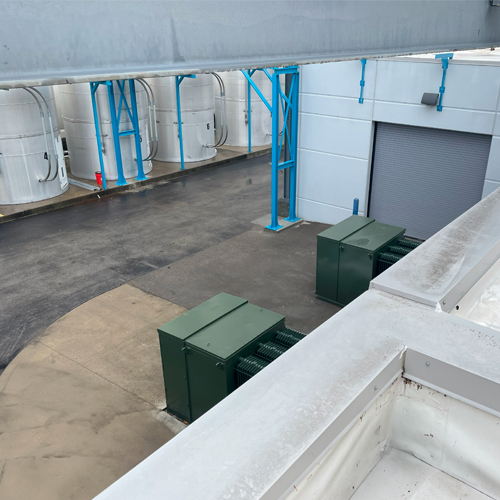
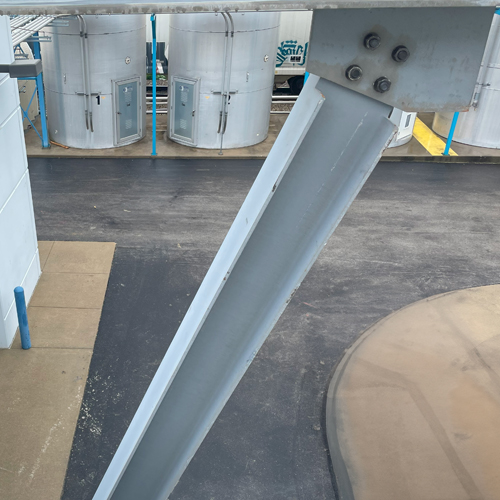
Second Solution
The collaboration between the manufacturer and VASEY extended beyond the initial solution. During an extremely harsh winter period with wind chills in excess of -40.0 °F, the existing facility’s chiller room encountered a catastrophic freeze, leaving their three chillers and ancillary equipment in ruins. Once again, the manufacturer turned to VASEY to mitigate the damage and restore operations. VASEY’s experts orchestrated a rapid “switch-over” piping process, spanning approximately 228 feet from the existing facility to the new, previously placed chiller. Despite the challenging weather conditions and time constraints, VASEY’s team executed the project swiftly, getting the client’s facility back up and running within four days, even working through the New Year’s holiday.
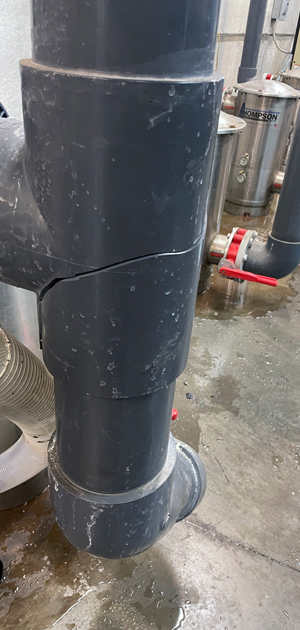
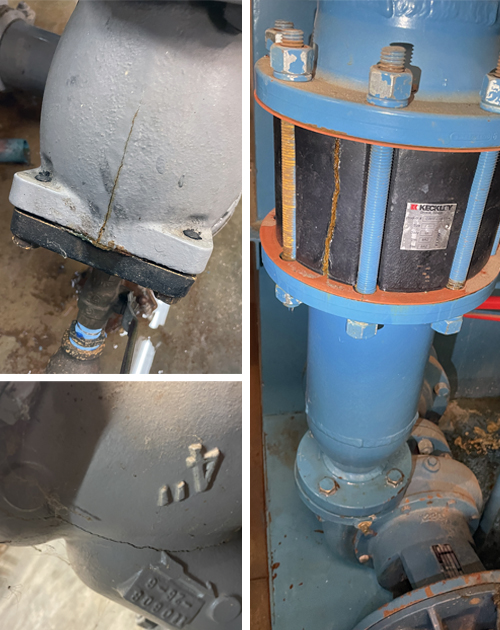
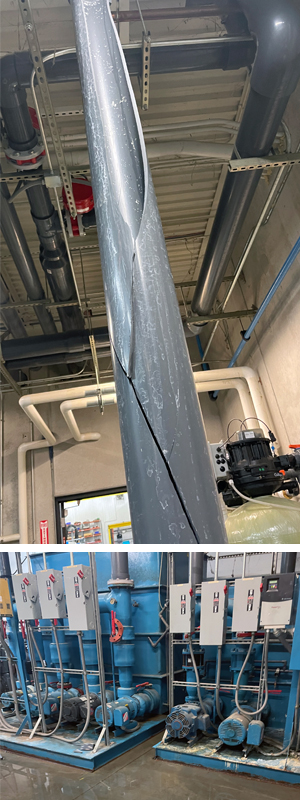
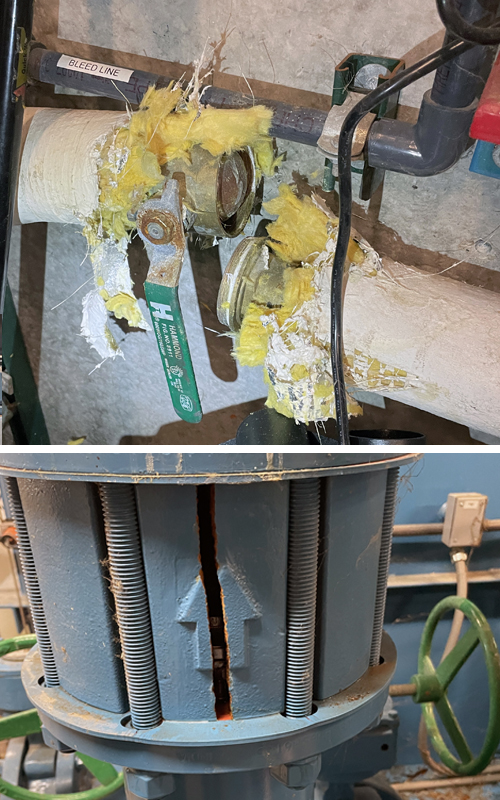
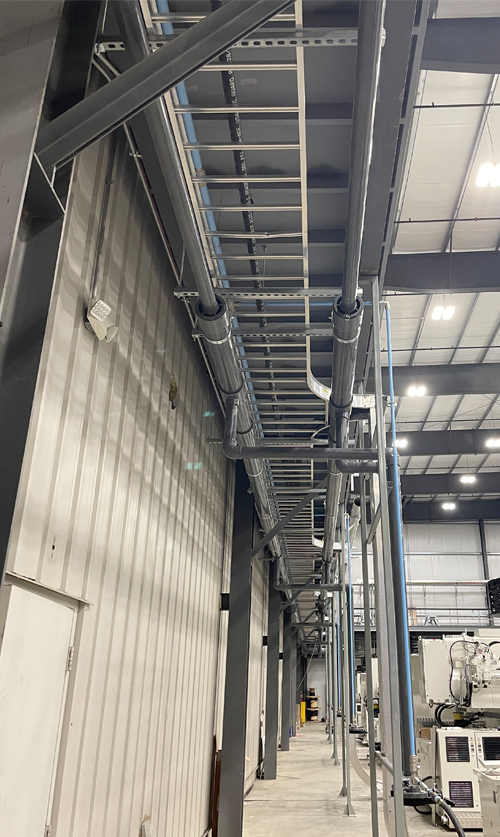
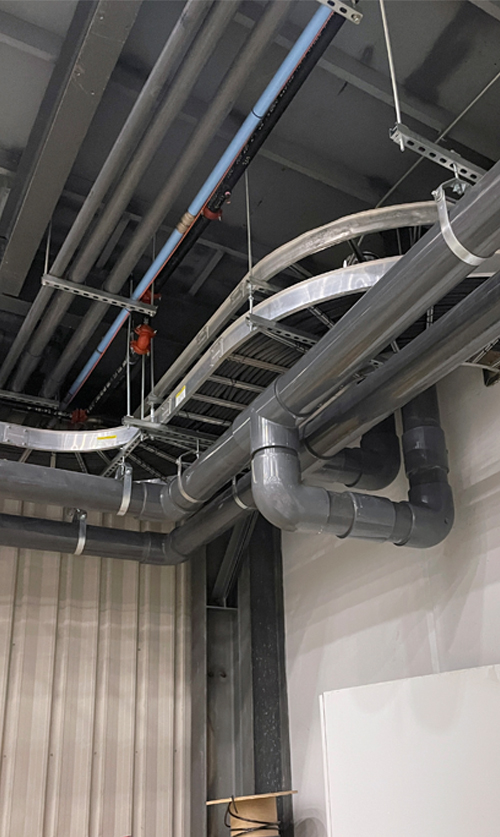
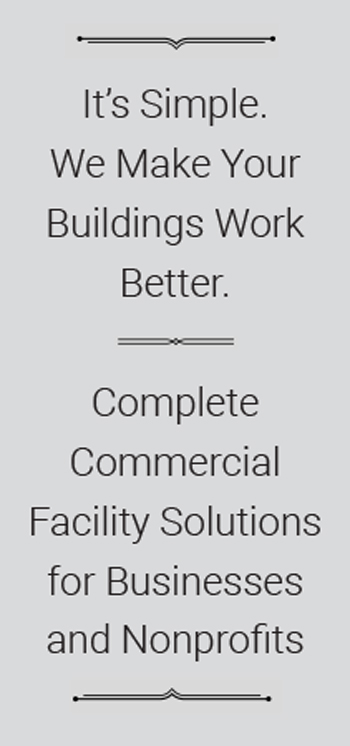

Call VASEY for a free consultation to determine how we might help you.
Contact Roger Mooney, VASEY Sales Manager, at
rmooney@vasey.com, or any
other sales team member.
Results and Impact
The partnership between the container manufacturer and VASEY illustrated their shared commitment to operational excellence and crisis management. The rapid deployment of temporary and permanent solutions ensured that their production lines remained active, averting potential missed shipping deadlines. The manufacturer’s intricate injection molding units, capable of producing hundreds of containers each day, were back in full operation, thanks to VASEY’s strategic interventions. The successful resolution of these challenges demonstrated the agility, expertise, and dedication of both organizations, reinforcing their position as an industry leader in sustainable logistics packaging.
Conclusion
The injection molding facility’s journey from facing a logistical crisis to a successful restoration of operations highlights the power of collaboration and innovation in the face of adversity. With VASEY’s assistance, they overcame significant obstacles and proved its unwavering commitment to delivering high-quality, sustainable products to clients across various industries around the globe. This case study underscores the importance of resilient partnerships and the ability to adapt swiftly to unforeseen challenges, ensuring the uninterrupted flow of critical manufacturing processes.