Creating a Portable, Safe and Comfortable Environment
When you go to the doctor, and she says, “You have cancer.” It is a traumatic and scary moment for the patient, followed by uncertainty. With more than 100 diverse types, Cancer is complicated to treat – whether it is managed by chemotherapy, radiation, or surgery.
Chemotherapy is a Cancer treatment that can have beneficial results for patients who use it. Creating chemotherapy compounds is a sophisticated process that requires precision and a strict adherence to safety for the individual compounding the chemotherapy agents. Many hospitals, especially smaller or remote facilities, may not have the capability to manage these dangerous compounding agents.
Additionally, every person’s treatment is unique to that individual. With chemotherapy agents having a short shelf life, treatments need to be prepared and administered almost at once by healthcare professionals in a fully sterile environment to ensure full protection of the person or persons inside.
To better protect those people making the compounds, effective December 1, 2019, the USP (U.S. Pharmacopeia’s) started enforcing stringent rules for the compounding of chemotherapy drugs, titled General Chapter <800>.
What Happens If:
- Your laboratory is down due to a fire or to equipment failure?
- Your hospital is smaller, and it does not have multiple labs to manage patient demands?
- You live in a rural area, and the closest facility for chemotherapy is five and a half hours away?
- A total laboratory remodel is necessary, and the existing lab must be dismantled in the interim?
VASEY Challenges
- Build sterile cleanrooms units to account for extreme temperature and humidity differentials since the modular units are leased anywhere in the United States. For example, a unit that is in Tampa, Florida, may be relocated to Seattle, Washington, within the next year.
- Circulate 100% outside air to prevent any cross-contamination, keeping the compounding teams safe.
- Make it with fully accurate temperatures, easily managed by work zone (hazardous compounding, non-hazardous compounding, and the general work area). A person stationed in a compounding room is covered from head to toe. As a result, their zones must be kept at a lower temperature since the gowns do not “breathe.”
- Make it sanitary with the ability to keep it perfectly clean according to USP <797> and USP <800> codes.
- Maintain tight air pressure tolerances. The location where the pharmacy technicians don their protective garments must be under positive pressure and sterile. The cleanroom itself must be at a negative pressure and sterile.
- Build-in energy efficiency and “green technology” to save money on operational costs.
- Standardize mechanicals for easy maintenance while meeting various federal and state codes.
Hazardous and Non-Hazardous Compounding Room Floorplan
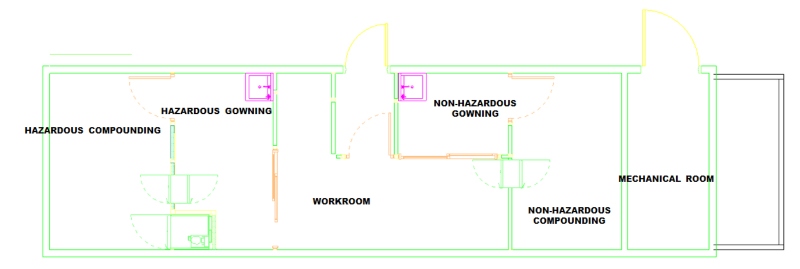
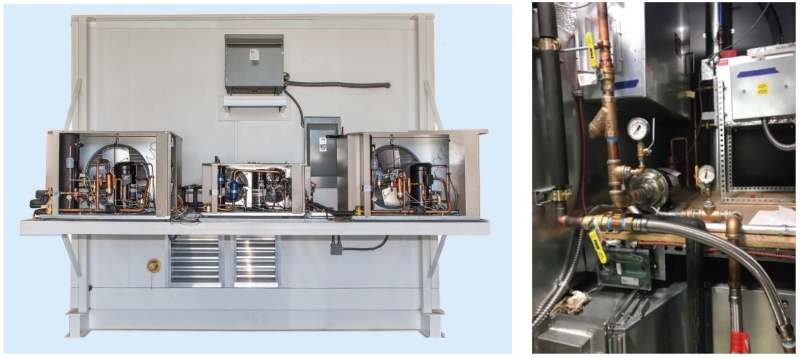
Schematic for all Mechanicals
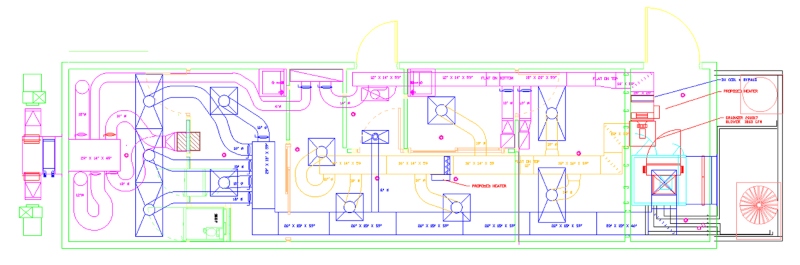
End Results by System
Non-Hazardous System
- 2,000 CFM airflow
- 1,900 CFM recirculated plus 100 CFM outside air for occupants
- Heat gain 14,000 BTU/hour
- Design dewpoint 50°
- Compounding and gowning rooms 62° to 65°
- Workroom 68° to 75°
- HEPA filter diffusers 1.0″ pressure drop
- Compounding positive air pressure
Hot Gas Bypass Valve
- Bypasses condenser with hot refrigerant gas directly to leaving side of the thermostatic expansion valve.
- Reduces compressor capacity since hot gas cannot change state and absorb heat
- Since gas is introduced before the TXV sensing bulb, the TXV also acts as a de-superheater to protect the compressor
- Maintains suction gas velocity for oil return
Heat Reclaim Coils
- Unit is 100% outside air
- Entering air temperatures from -20° to 120°
- Exhaust air +/- 65° or less
- Testing revealed 0° entering air could be heated to 41° with just exhaust heat, and 97° air could be pre-cooled to 88°
- Glycol is bypassed around outside air coil if glycol is less than 35° to prevent frosting of the exhaust coil
Hazardous Compounding Cleanroom Design Conditions
- Compounding in an ISO Class 2 biosafety cabinet (BSC)
- Biosafety cabinet in an ISO Class 5 room under negative pressure relative to surrounding spaces
- Gowning in an ISO Class 8 cleanroom positive pressure relative pressure to surrounding spaces
- Target room temperature 62° 50% RH with a max temperature of 68° 55%
Hazardous System
- 2,400 CFM airflow and 100 CFM to non-hazardous rooms
- 100% outside air
- Internal heat gain < 10,000 BTU/hour
- Outside air load > 130,000 BTU/hour
- Design dewpoint 50°
- Compounding and gowning 62° to 65°
- HEPA filter diffusers 1.0″ pressure drop
- Compounding negative air pressure
Exhaust System
- Duplex exhaust fans with automatic startup on failure of a lead fan
- 2,390 CFM at -2.5″ WC
- Keeps module 50 CFM positive
- Exhaust stacks 4’0″ above the roofline
- No loss – stacks discharge exhaust vertically for added safety around the unit while draining water away from the fan
Bio-Safety Cabinet (BSC)
- Single-pass 100% exhaust
- 100 FPM minimum air velocity into BSC
- Work access into BSC plus or minus 8 square feet
- Exhaust flow 800 CFM
- Make-up air 750 CFM
- From gowning 50 CFM
- Room size 8′ x 6-1/2′ x 7′-9″ ceiling = 403 cubic feet
- Air change every 30.22 seconds
Hot Gas Reheat Valve
- Bypasses condenser sending hot refrigerant to a coil on the leaving side of the evaporator coil.
- The condensing hot gas heats the discharge air
- The condensed refrigerant is delivered to the inlet of the liquid line solenoid valve
- Allows DX coil to run “cold” enough to dehumidify and heats air to avoid overcooling space without using electric reheat.
- The super subcooled liquid refrigerant from the reheat coil further sub-cools the liquid from normal condenser increasing efficiency
Construction
- All rooms have airlock access
- Access doors: interlocked so only one door open at a time
- Material pass-through: air locked with HEPA filtration of air inside pass-through
- Walls: FRP covered for cleaning and sanitation
- Floors: molded with cove edges to allow cleaning into corners
- Ceiling: FRP “sealed” plenum
Air Locks
- All rooms have airlock access
- Access doors interlocked, so only one door opens at a time
- Material pass-throughs air locked with HEPA filtration of air inside pass-through
The dynamic trio, VASEY Commercial Facility Solutions, Modular Devices, and Cleanroom Design developed the perfect solution – a compact, modular, drop-in-place, plug-and-play sterile cleanroom facility – capable of being easily transported to any location within the United States. While each company focused on its core ability, VASEY designed, engineered, and installed the HVAC system and mechanicals.
Things to Make It All Work
- Circuit “A” of the hazardous unit has a 38-pound liquid receiver to hold refrigerant for heat reclaim coil
- Compressor operation required at 50° ambient to dehumidify
- Full low ambient fan speed control on condensing units
- 15 KW electric humidifier to prevent static electricity
- Steam condensate coolers
- Variable speed drives on all blowers
- Smoke detectors
- Fire sprinklers
- Electric reheat for workrooms
- Electric heat in the mechanical room
- Electric phase monitor
- Remote access computer control
- Mechanical Room (4 ft wide x 6 ft. long x 9 ft. tall)
- All necessary ceiling pipe and ductwork is contained in a space 7.0″ or less
- The mobile units are about 48′ x 14′ or 30′ x 14′ to fit on a semi-trailer for transport.