Overview
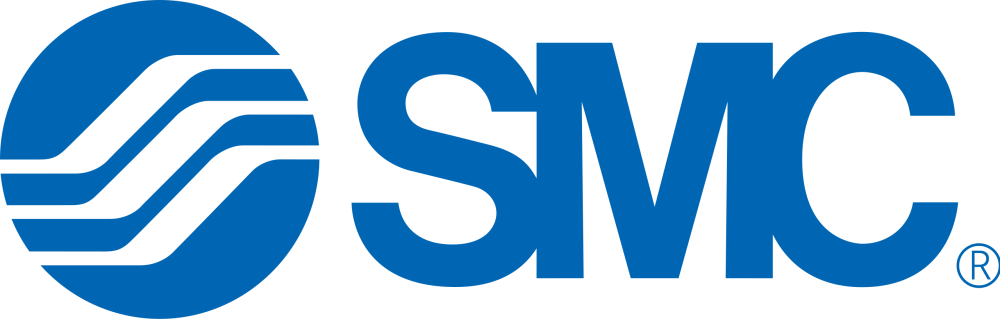
SMC Corporation of America, a global leader in pneumatic technology, has a recognized history of driving automation and innovation. With a steadfast commitment to delivering superior products and services, SMC has established itself as a trusted partner in the industrial automation sector.
This case study explains VASEY’s custom engineered nitrogen testing solution for SMC’s ISO-classified clean room environment. The partnership between SMC and VASEY exemplifies their dedication to precision engineering and quality control.
Challenges for Quality Control
The task at hand, to design a cutting-edge nitrogen-based pressure decay leak test system for SMC’s automation components, including pressure regulators and valves. The challenge was twofold: achieving ultra-purity, zero contamination in a high-pressure piping system and devising a testing solution that accommodated diverse components seamlessly.
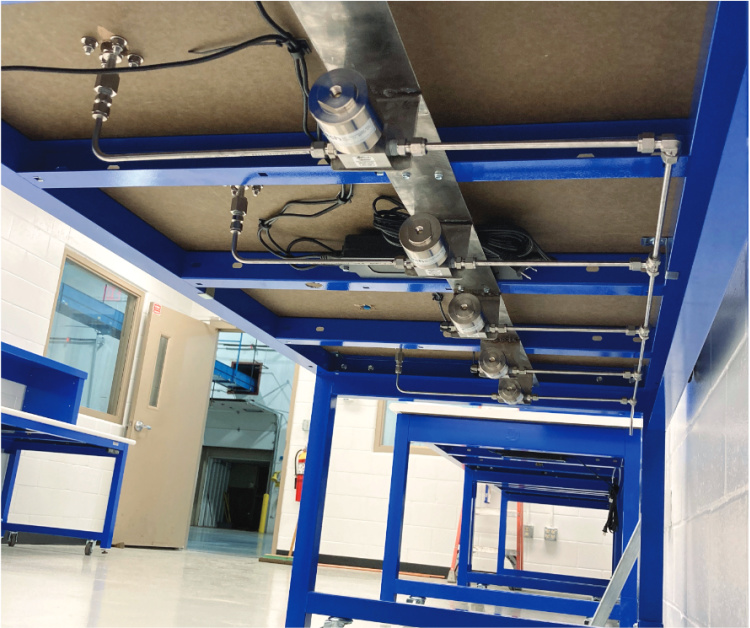
VASEY’s Engineering Expertise
To surmount these challenges, SMC turned to VASEY to craft the ideal solution. Recognizing the need for a clean room compliant setup, VASEY engineered vital solutions that aligned seamlessly with SMC’s stringent specifications. This approach addressed concerns of contamination and ensured that the testing environment met the highest industry standards.
Precision Piping for Nitrogen Testing
One of the central components of this project was the intricate piping system required for pressure decay leak testing. VASEY and the SMC team collaborated closely to design and implement a piping network capable of handling nitrogen pressures ranging from 1500 psi to an impressive 3000 psi across eight testing stations. This network facilitated accurate and comprehensive quality control testing for SMC’s automation components.
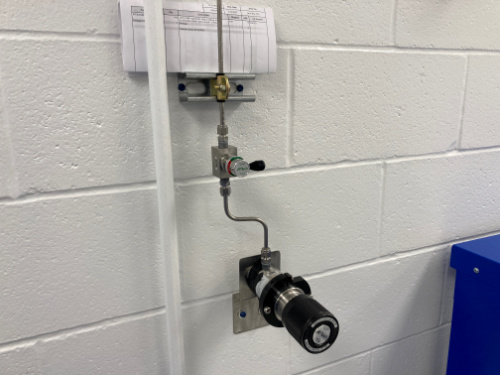
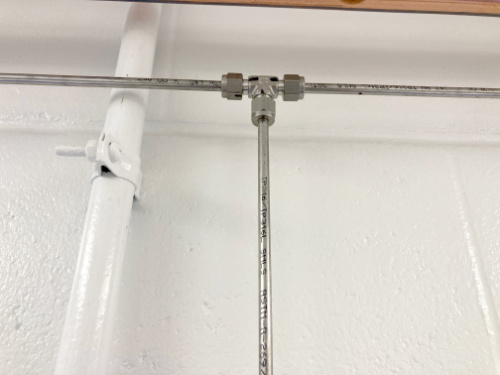
Mitigating Corrosion and Maintaining Aesthetics
Managing the corrosive nature of nitrogen required careful consideration. To prevent potential harm and maintain an aesthetically pleasing environment, the drainage system was engineered to avoid splashing and potential hazards. Additionally, vent lines were integrated to expel trapped air from the pipes, ensuring smooth flow and preventing disruptive gurgling sounds. A strategically placed check valve facilitated efficient drainage, ensuring no residual waste remained in the pipes during subsequent test cycles.
Positive Outcomes
Through clear communication and collaborative efforts, SMC and VASEY successfully realized a sophisticated nitrogen testing and quality control system. This achievement not only reinforced SMC’s reputation as an industry front-runner but also highlighted their unwavering dedication to innovation and precision engineering. The project’s resounding success positions SMC to continue delivering advanced automation solutions while adhering to the highest standards of quality and performance.
Uniformity and Flexibility
A hallmark of the project was the emphasis on uniformity and flexibility. VASEY’s expertise and mindfulness shone through as every test station was precisely the same, even down to the uniform length of piping. Each section of piping was skillfully fabricated to ensure a standardized volume of stored nitrogen. This uniformity eliminated variables and allowed for precise assessment of pressure leakage, contributing to consistent and reliable results.
SMC required flexibility. Penetrating up through the test stand base, VASEY engineered a threaded stub in order to handle SMC’s different adapters in order to test their various sizes and types of components.


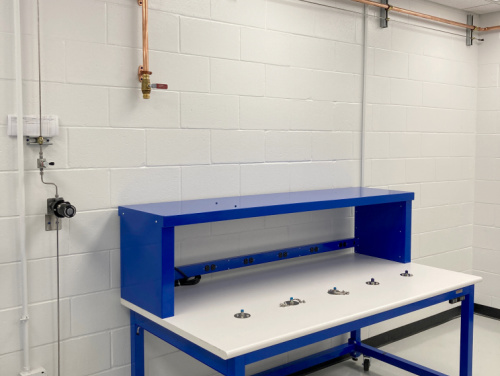
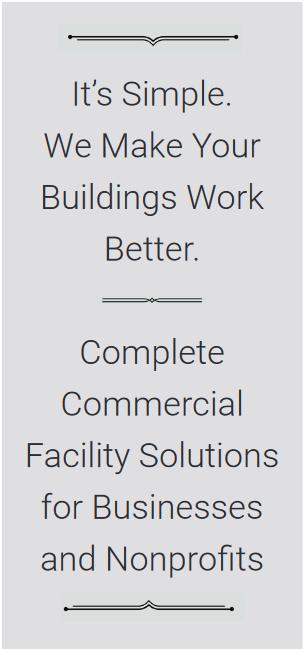
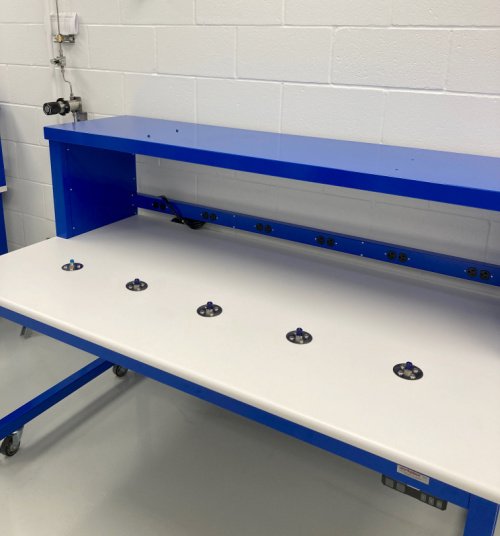
Conclusion
The partnership between SMC and VASEY exemplifies their commitment to innovation, precision, and quality. By addressing intricate engineering challenges and incorporating versatile design features, VASEY successfully constructed a safe, high-pressure nitrogen testing and quality control system. This case study underscores VASEY’s role as an industry leader, creating enhanced solutions and resource efficiency while upholding rigorous standards of quality and performance.